Quality, delivery date and price have always been the most concerned issues of customers in precision parts industry. Under the condition of the same quality and price, customers attach great importance to delivery date
How to high-efficiency and precision parts is the tireless pursuit of Gree Dajin mould. The early processing cycle of spiral, helical gear and shaft parts is long (10 days) and the cost is high. Although the quality was highly recognized by the customer, the delivery date could not meet the customer's requirements. Gree Daikin analyzed the processing, combined with the process improvement, changed the electric punching processing of the model peripheral oil groove and positioning pin hole to CNC processing, so that the processing time changed from 36h to 6h, saving 30h processing hours. The machining strategy and parameters are optimized, so that the EDM machining strategy is modified from 2 rough and 3 fine to 2 rough and 2 fine, and the finishing roughness of machining parameters is changed from Ra0 eight μ Change to ra1 0 μ, A total of 42h of processing time is saved. Moreover, on the premise of ensuring the quality, the electrode material is changed from tungsten copper to imported red copper, which not only achieves the same effect, but also saves the cost of electrode material.
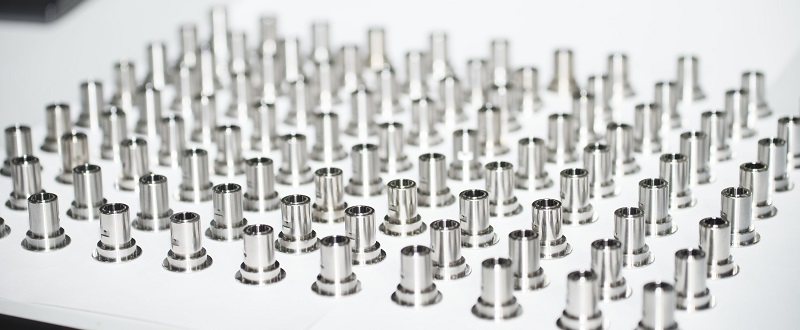
|