Application of DLC coating on moving parts of injection mold to improve mold resistance
In the past, the mold resistance of moving parts is a difficult problem, which is usually treated by nitriding or quenching. However, when there is a large number of molds, such as 800000 to 1 million molds, this process can not meet the requirements of wear life.
DLC is a relatively new process, which is composed of carbon and similar in nature to diamond. Due to its high hardness, high elastic modulus, low friction coefficient, wear resistance and good vacuum tribological properties, it is very suitable for wear-resistant coating.
The traditional vacuum evaporation coating method has high deposition speed and high purity, but the bonding strength between the film and the substrate is poor. The ion implantation method is firmly combined with the matrix, and there is no adhesion fracture or peeling on the surface. However, the implantation layer of ion implantation is too thin, only hundreds of nanometers, which limits its application under wear-resistant conditions.
In order to overcome the problems of poor adhesion of vacuum evaporation coating method and shallow implantation layer of ion implantation method, vacuum evaporation ion beam assisted deposition technology is combined with thin film evaporation deposition and ion implantation technology. In this technology, the elements are deposited on the substrate with evaporation source (electron beam) and the coating is bombarded with ions to obtain a high-performance dense film thicker than the ion implantation layer and greater adhesion than the evaporation coating method.
After vacuum evaporation ion beam assisted coating, a smooth and compact DLC film is formed. The DLC film reduces the friction coefficient of the matrix material and improves the tribological properties.
The following legend is the application of oblique top DLC layer. Good performance results are obtained.
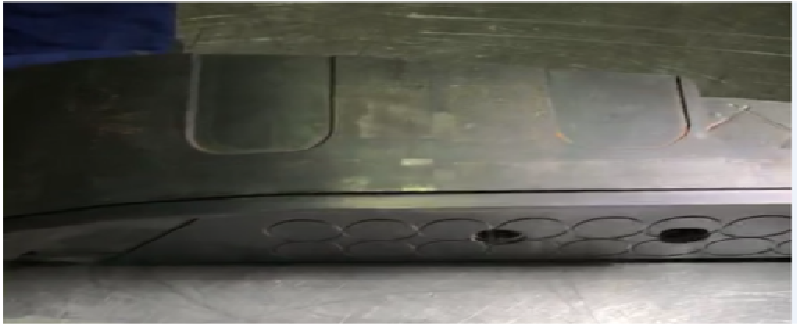
|